Written by Capt. Jordan Hempker
When building hose and nozzle packages for Engine Company operations, most fire departments focus on testing flow rates, comparing nozzles, and determining optimal stretch lengths.
These are critical considerations—and a solid Engine Company deployment model should answer them. But there’s one small detail that often gets overlooked, despite its outsized impact on the fireground: The Pony Tail.
It goes by many names. Firefighting is a local business—what one department calls a pony tail, others may refer to as a stub line, whip line, pig tail, or preconnect extension line. For clarity and consistency in this article, we’ll use the term “Pony Tail".
But regardless of what your crew calls it, the purpose is the same: to create a smoother, safer, and more efficient connection between your pump discharge and attack line.
What Is the Pony Tail?
The pony tail is a short section of hose—typically 6 to 15 feet long—used to connect the pump discharge to the main attack line.
It’s commonly used in crosslay or speedlay configurations, helping move the working line away from the side of the pump panel and reducing congestion during initial deployment.
This setup can also be applied to engines pulling lines from the tailboard. A well-designed pony tail system positions the first coupling away from the hose tray and pump panel, allowing for a cleaner workspace for the pump operator, reduced tripping hazards, and more efficient loading and deployment of the line.
Advantages of Adding the Pony Tail
No two engines are the same. And not all discharge elbows are created equal. Styles vary—some are fixed, others swivel—affecting how hose deploys from the pump. Many departments connect the attack line directly to the discharge port, which can present challenges depending on hose characteristics.
When engine companies deploy attack lines from the tailboard, the discharge is typically located in one of two places: an exposed elbow at the rear of the apparatus body or a discharge fitting located toward the front of the hosebed near the pump.
In either configuration, incorporating a properly sized pony tail offers clear advantages by:
- Maximizing the usable length of the attack package, increasing the amount of working line that clears the bed and improving deployment efficiency
- Giving the hose a gradual bend—reducing turbulence and flow disruption.
- Minimizes the risk of kinks at the discharge, especially with lower pressures or less rigid hose.
- Allows for easy line extension, with the first coupling moved away from the pump panel or tailboard
- Makes disconnection easier, letting firefighters drop the line from ground level—no climbing, no wasted time.
And the extra 6-15 feet? It can be a game-changer when stretching to the opposite side of the engine or trying to get that first length past the tires.
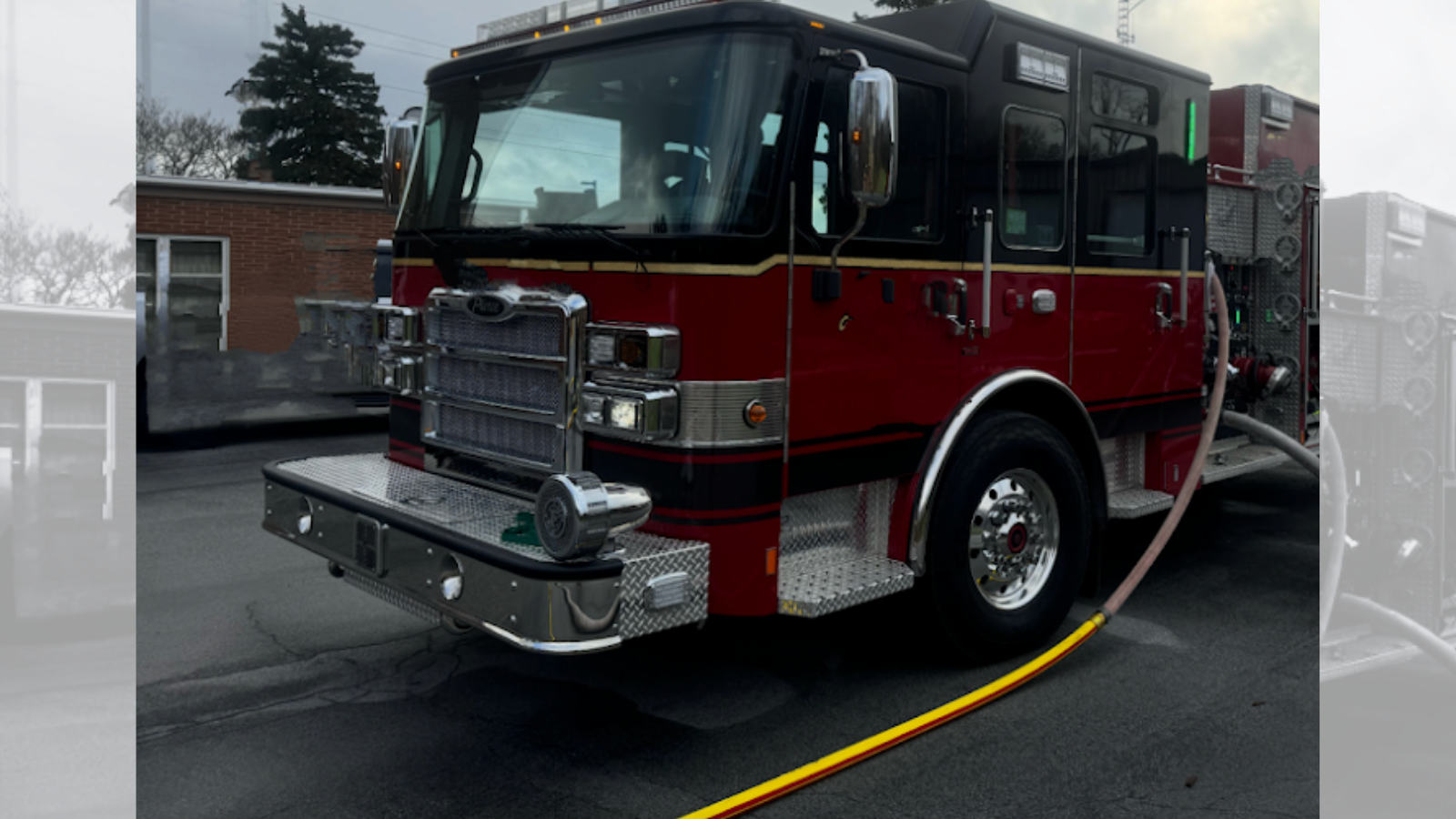
CONSIDERATIONS WHEN USING A PONY TAIL
When properly fitted and paired, a pony tail offers operational advantages. However there are important considerations that are often overlooked when put into practice:
- Excessive Length and Poor Fit
A pony tail that is too long may not fit properly in the designated hose tray. Thus, it can result in tight folds or excessive bends, increasing the chance of the hose becoming jammed during deployment. An overloaded tray may also sit too high or interfere with other equipment, ultimately reducing the ability to deploy the entire attack line smoothly.
- Ergonomic Limitations
Some pump panel and plumbing designs are not ergonomically configured to support easy reloading when a pony tail is in place. Awkward discharge angles or tight spaces can make it difficult to repack or reload the line efficiently, especially during high-tempo operations or post-incident cleanup
- Use of Old or Mismatched Hose
Departments often use older hose for pony tails due to cost savings or convenience—sometimes even transferring hose from older engines to new ones. However, older or mismatched hose may:- Lack kink resistance
- Restrict flow at the discharge due to a smaller ID compared to the rest of the attack package
- Have mismatched diameter, stiffness, or wear that can introduce failure points or inefficiency at the discharge
- Be incompatible with low-pressure modern attack packages (e.g., designed for 100 psi, not for 50–75 psi
Standardization is the key. If a pony tail is going to be used, it should be made from the same hose as the rest of the attack package. This ensures consistent flow characteristics, minimizes kinks, and maintains overall performance from discharge to the nozzle.
However, A PONY TAIL DOESN'T ALWAYS FIT
I've highlighted the advantages offered by incorporating a pony line – however, I want to offer a word of caution. While a pony tail has its place on many rigs, it doesn't always deliver optimal performance and may not work for every department. Here is a real-life example of when a pony line hindered rather than helped:
In my department, we run engines equipped with slide-in trays for our speedlays. Originally, with a high-pressure setup, the hose sat lower in the tray and maintained a low profile while in the “pump house.”
Due to the recessed and difficult-to-reach discharge elbows, we used a pony tail section to assist with the connection and provide an easily manageable line for repacking after training or fire incidents.
As we transitioned to a modern low-pressure attack system, we began noticing several deployment issues. First, the new hose sat higher in the tray – combined with the pony tail, it increased stack height and made it difficult to deploy cleanly. This also caused the hose to bunch up when the tray was slid into place. The hose often became snagged and couldn’t be placed into service smoothly.
The critical issue was that the pony tail did not match the hose used in the rest of the low-pressure attack package. The older hose section had reduced kink resistance, a different inner diameter, and incompatible material characteristics.
The result? Reduced flow at the nozzle. Poor performance in the field.
After several weeks of testing and reconfiguring the entire attack package, our department decided to remove the pony tail and connect the line directly to the discharge. This change improved deployment reliability, reduced the potential for snags, and restored intended flow performance.
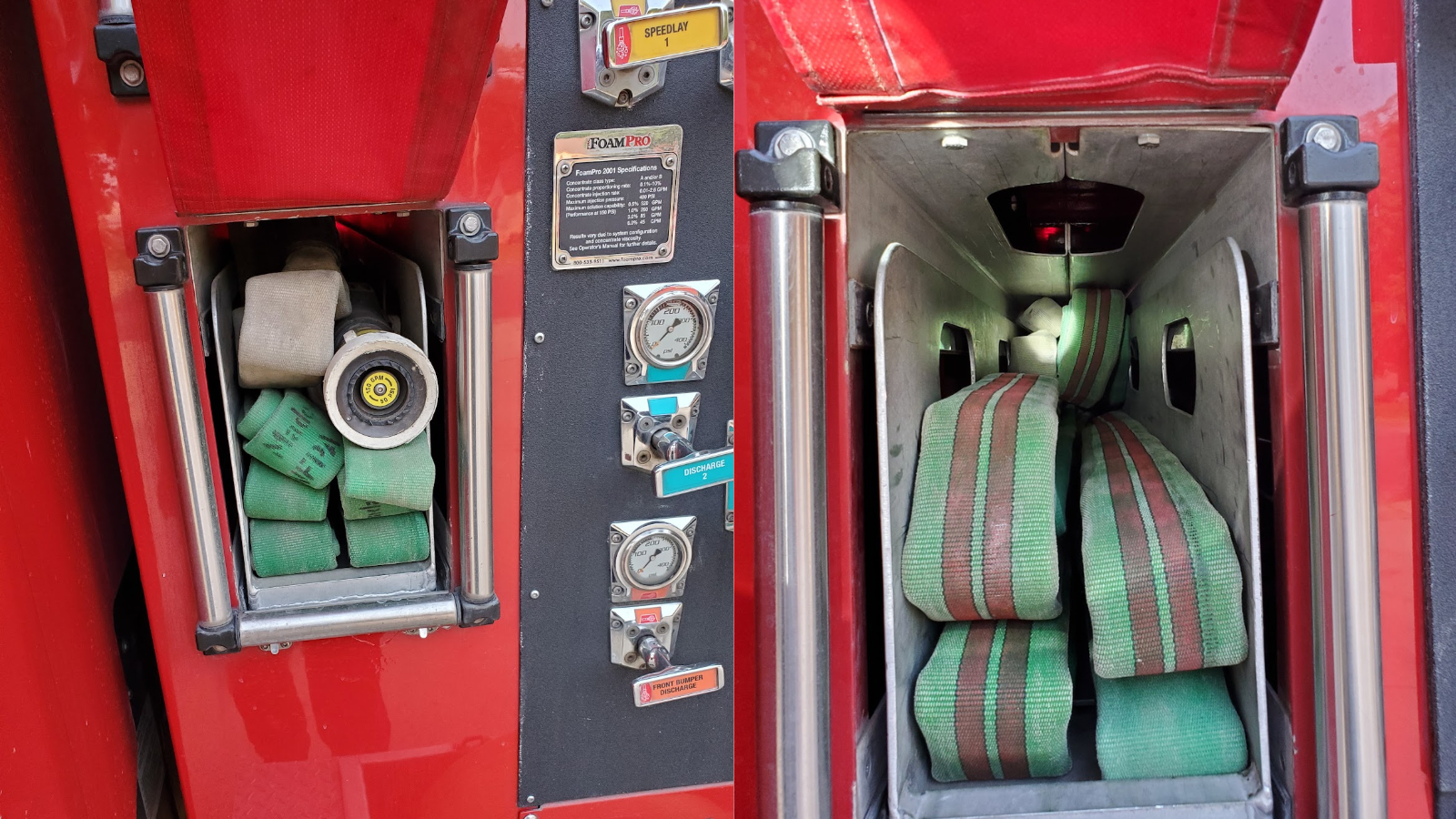
The Takeaway: Small Section, Big Impact
Every piece of the hose line matters—from the pump panel to the nozzle. The pony tail is part of the overall hose attack package.
- Evaluate the package as a whole. As we systematically evaluate our hose lines for performance, the pony tail must be included in that assessment.
- If it’s in the line, it should be in your testing. When flow-testing or performance-testing preconnects—whether 200 feet or any length your department uses—it’s important to include the pony tail in the measured layout if it’s part of the system.
- Have you accounted for the added length? Remember that the pony tail adds to the overall length of the line, so we must account for that addition for our friction loss.
- Does it meet your operational goals? For the pony tail section to be successful within the entire attack package, it must meet operational goals for kink resistance, provide a hazard-free workspace for the pump operator, allow for easy hose reloading without compromising deployment, and avoid negatively impacting GPM flow or pressure.
Engine model deployment is never static; it should be constantly reviewed and refined for efficiency. And most importantly, it’s okay to change or improve things based on operational feedback, testing, and real-world experience.
Because the fireground doesn’t care what your spec sheet says—only how your hose performs when it counts.
About the Author:
Captain Jordan Hempker is an 18-year fire service veteran with experience in rural and suburban operations. He currently serves as a shift commander with Harrison Township Fire Department in central Ohio, where he focuses on adapting engine company tactics for limited staffing and diverse incidents. His approach emphasizes tactical clarity, aggressive operations, and leadership that meets today’s fireground challenges.
Jordan began his career as a volunteer firefighter, proudly serving for 10 years while gaining valuable experience across multiple part-time departments. He later served full-time with Shawnee Township Fire Department and American Township Fire Department, both located in Lima, Ohio.
He owns and operates Western Buckeye Training, a fire service training company focused on modern, mission-driven operations. In addition, Jordan is a consultant for Mercedes Textiles, contributing to training and education on fire hose and attack packages across North America. Jordan is married to his wife, Brittany, and they share their home with three dogs. He also takes great pride in being an uncle.